Cleaning with low-pressure plasma
Ultrapure surface cleaning
Clean and reliable method
Surface cleaning in industry plays an important role, e.g. for improving coating adhesion.
With wet-chemical cleaning methods traces of detergent or solvent are left on the surface, which even after thorough rinsing and drying are not completely removed.
However, low-pressure plasma cleaning results in surfaces free of organic contamination. Treatment cycles of just a few minutes give outstanding results with no surface residues.
The excellent crack penetration of low-pressure plasma is advantageous. This means that even intricately formed parts are perfectly cleaned since the gas also penetrates into small gaps that liquids cannot reach.
The decisive factor in the plasma cleaning process is the formation of gaseous and hence volatile products that can be removed from the process chamber without any problems. The plasma components react with the organic contamination and degrade it to water and carbon dioxide even at room temperature:
(-CH2-CH2-)n + 3n O2 " 2n CO2 + 2n H2O
Classification of cleaning procedures
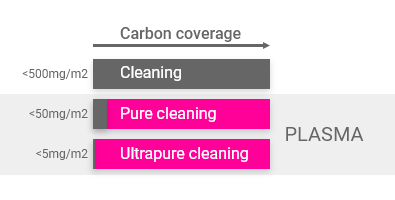

Advantages of plasma cleaning
- Extremely clean surfaces (ultrapure cleaning)
- Low treatment temperature
- High crack penetration
- No subsequent drying necessary
- No detergent residues
- No waste disposal costs
- Low operating costs
- Eco-friendly process

Areas of application
- Optical industry
- Microelectronics
- Chip card production
- Electrical engineering
- Glassware industry
- Metalworking industry
- Watch industry
Example
Leadframe treatment
For sufficient adhesion of the bond wires and chips to leadframes, the surface has to be as clean as possible. Adhesion is dramatically reduced by organic contamination and often prevents achievement of the desired adhesion quality. Because of the uneven contamination, leadframes have to be cleaned in their entirety. The process of low-pressure plasma cleaning is particularly suited to this, as fully loaded leadframe magazines can be cleaned without difficulty thanks to plasma’s high mobility.
Read more: Leadframe treatment, PDF 218 KB More examplesProduction integration options
Intelligent automation engineering allows plasma systems to be integrated into production lines.
Selecting suitable pump systems allows evacuation times to be reduced to such a degree that cycle frequencies can be matched to application requirements. In addition, modularly designed systems allow a quick and flexible respond to production expansions.
Which materials are not really suitable for low-pressure plasma cleaning?
All materials causing a significant disturbance of the vacuum and / or plasma because of emission. This applies to some silicones and fabrics.
Plasma processes are hardly suitable for inorganic contaminations. However, workpieces with both inorganic and organic contaminations can be cleaned in combination with wet-chemical pre-cleaning.
Materials suitable for low-pressure plasma cleaning
All vacuum-proof and plasma-resistant materials like e.g. most of the plastics, metals, glasses, ceramics, caoutchouc / rubber, even foam materials.
Bondability
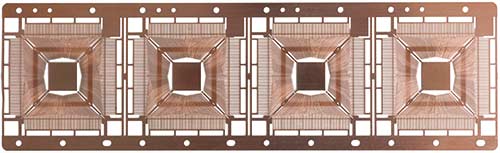
Cleaning in low-pressure plasma improves the bondability significantly